The capitalization of companies consistently working on environmental aspects is 10-12% higher than the industry average. In addition, these companies are more attractive to talent.
«BCG Ecology Review 2021»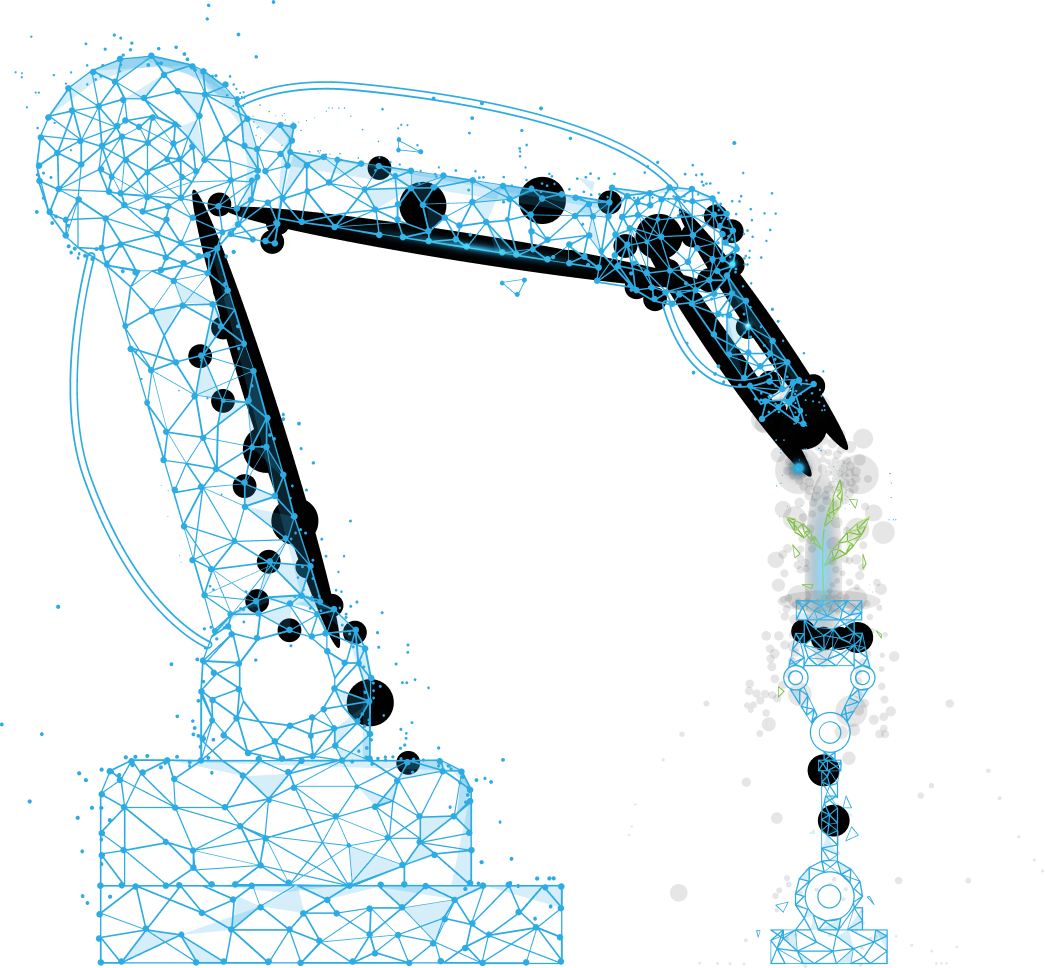
GHG Emissions and Industry
Industrial companies recognize the need to reduce their carbon footprint, with more than three-quarters considering decarbonization as a high priority.
Industrial companies have enormous carbon footprints. Their production and logistics operations account for more than half of global carbon dioxide (CO2e) equivalent emissions from energy and fuel source consumption. Considering current trends, emissions from Industry would need to decrease by approximately 45% by 2030 to meet the parameters of the Paris Agreement’s 1.5°C target for limiting the rise of global temperatures.
With this in mind we’re dedicated a lot of research and development to finding ways to assist our clients with monitoring, reducing, and counter-acting their GHG emissions in the pursuit of carbon neutrality. The result is a selection of digital solutions and operational changes that can be made to business practices.
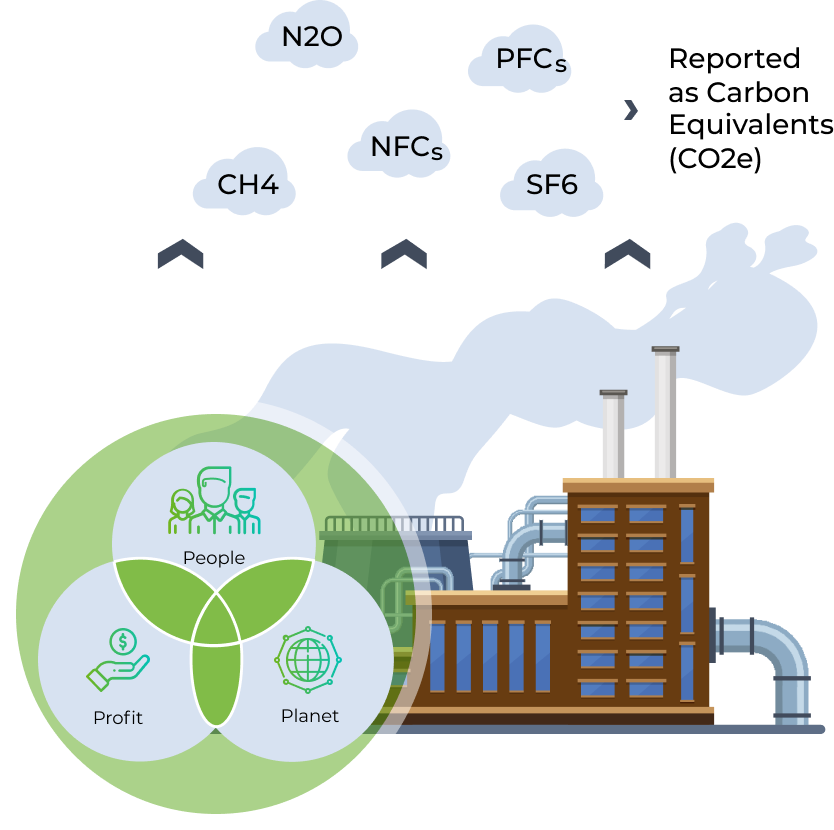
Companies can take action that mutually benefits the environment and creates financial value.
Reducing greenhouse gas emissions doesn’t have to be an expensive endeavor. Here are some steps to help companies reduce their GHG emissions from operating activities.
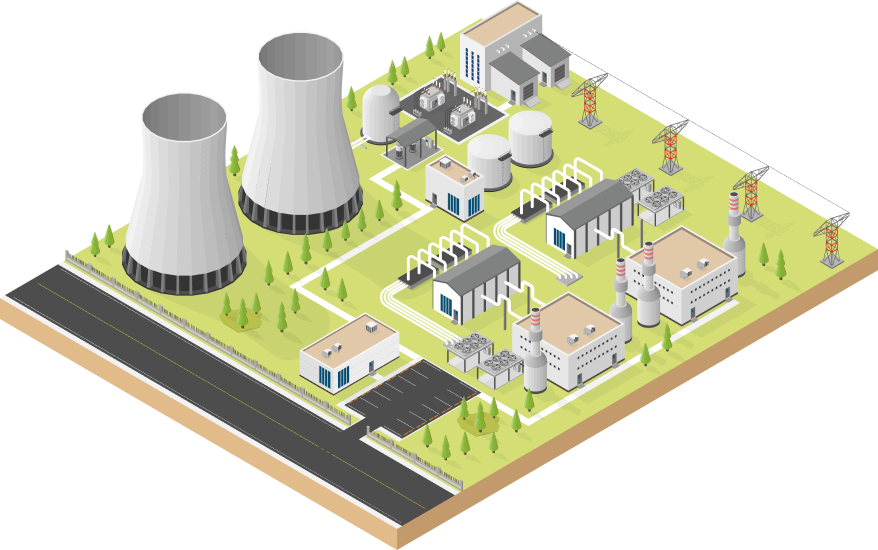
- STEP1Carbon footprint assessment
Eco monitoring and a clear understanding of GHG emission levels.
To assess and reduce their carbon footprint, companies can implement systems for monitoring, managing, and dispatching energy consumption
- STEP2Defining real goals
Increasing efficiency
- Reduce energy consumptionA company can avoid generating emissions by improving its energy efficiency, changing its operations, and changing how it supplies energy to its operations.
- Reduce idling equipment timeUsing a power breaker, for example, would switch off equipment during periods of inactivity, saving energy while setting up a positive air pressure system simplifying the search for leaks.
- Simplify / reduce logistical processesUsing route optimization, effective planning, and automated control systems.
- Recycle and remanufacture
- STEP3Determining specific action and solution options
- Optimize logistics networks = chains to minimize the distances traveled.
- Optimize material handling through intermodal transportation.
- Replace conventional fossil-based power with renewables.
- Replace truck transportation with rail or ship.
- Capture process-related carbon byproducts, and reuse them in chemical processes.
- Produce the equivalent of a new product by reusing parts from used and returned products (remanufacturing).
- Replace high-emission processes and technology with low-emission substitutes.
- Optimize equipment and building energy and fuel efficiency (including heat recovery).
- Use 3D printing to minimize resource waste, packaging, and transport emissions.
- Deploy energy monitoring and management systems to reduce consumption.
- Apply operational excellence levers to reduce scrap and other waste.
- Establish a closed-loop system to recycle and reproduce parts and products.
- Replace fossil-based fuels with biofuels, biomass, or other fuels.
- Compensate for carbon emissions through offsetting measures such as reforestation.
We have a set of products that assist industrial operations
with managing their carbon equivalent emissions
Environmental emissions and hazardous gas monitoring system at one of the world’s largest Downstream Plants
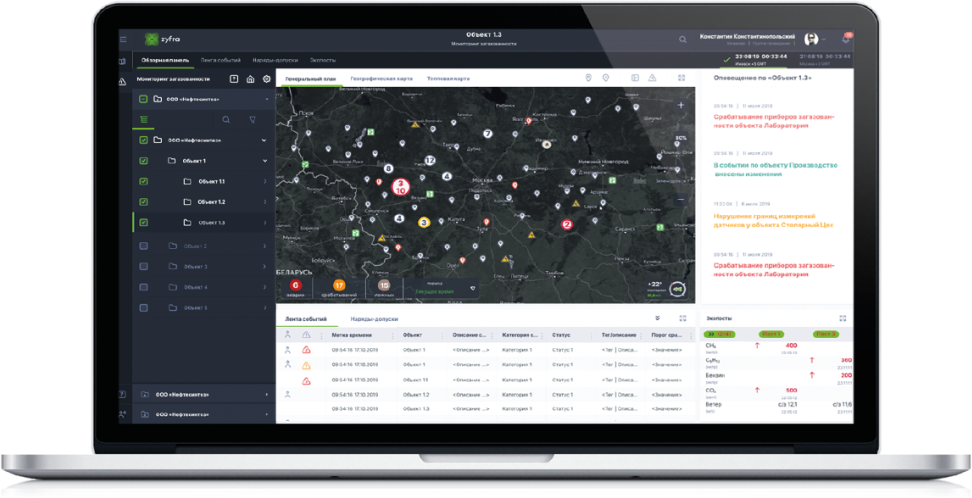
- Reduced gas leak detection time by 40-50%
- Reduced emergency response times by 12 hours
- Reduced gas sensor false alarms by 20%
- Automated gas contamination control, reducing human intervention by 90%
Energy Efficiency Management System
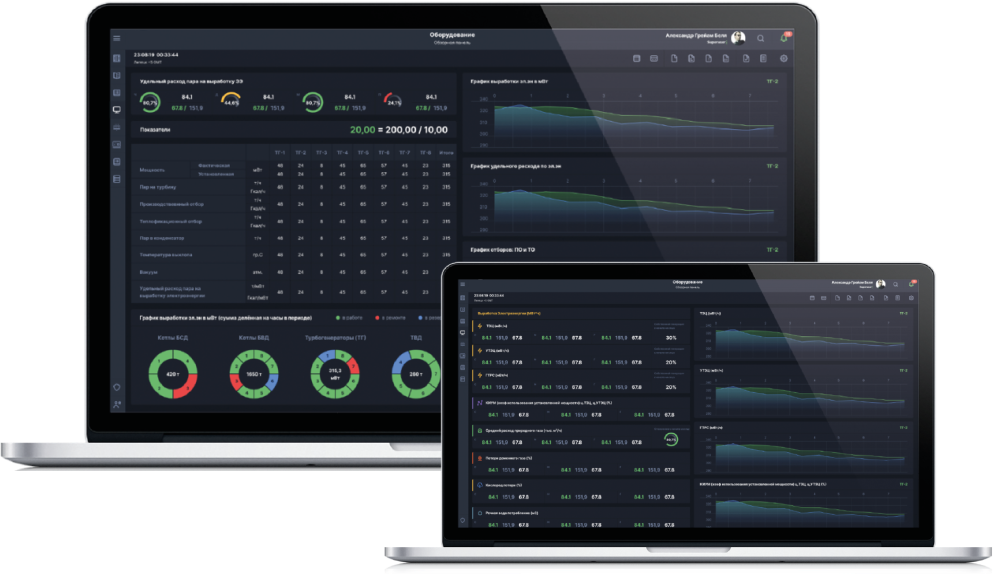
Design and deployment of an Energy Efficiency Management System to monitor all energy sources in real-time, identify and report losses, provide analytics for the development and implementation of energy-saving measures, and increase the reliability of energy-generating equipment.
RESULTS ACHIEVED:- Reduced energy consumption by 1.8%
- Reduced purchased gas consumption by 1.5%
- Reduced product losses by 1.2%
Zyfra Mining has introduced and continues to improve and expand on a series of solutions that increase operational efficiency, thus reducing waste and excess GHG emissions
Combining multiple solutions into a single ‘Intelligent Mine’ is something we’re very proud of. We built such an Intelligent Mine for one of the world’s largest integrated energy companies — a leader in coal, heat, and electricity production and one of the largest railcar and port operators in Russia — who have worked with Zyfra Mining and our Intelligent Mine to increase productivity in their mining and transport complex. More efficient vehicle and equipment use results in lower GHG emissions. Diesel combustion emissions decreased by 10% Annual savings of USD 13.5 million a year.
RESULTS ACHIEVED:- Diesel conservation of up to 10%
- Increased mileage rate utilization by 7.6% due to reduced idle periods
- Increased productivity by 12.7% in terms of traffic volumes and 19.2% in terms of freight turnover
- Reduced excavator energy consumption per cubic meter of rock mass by ≈ 30%
- Reduced losses from fuel misuse by 7-15%
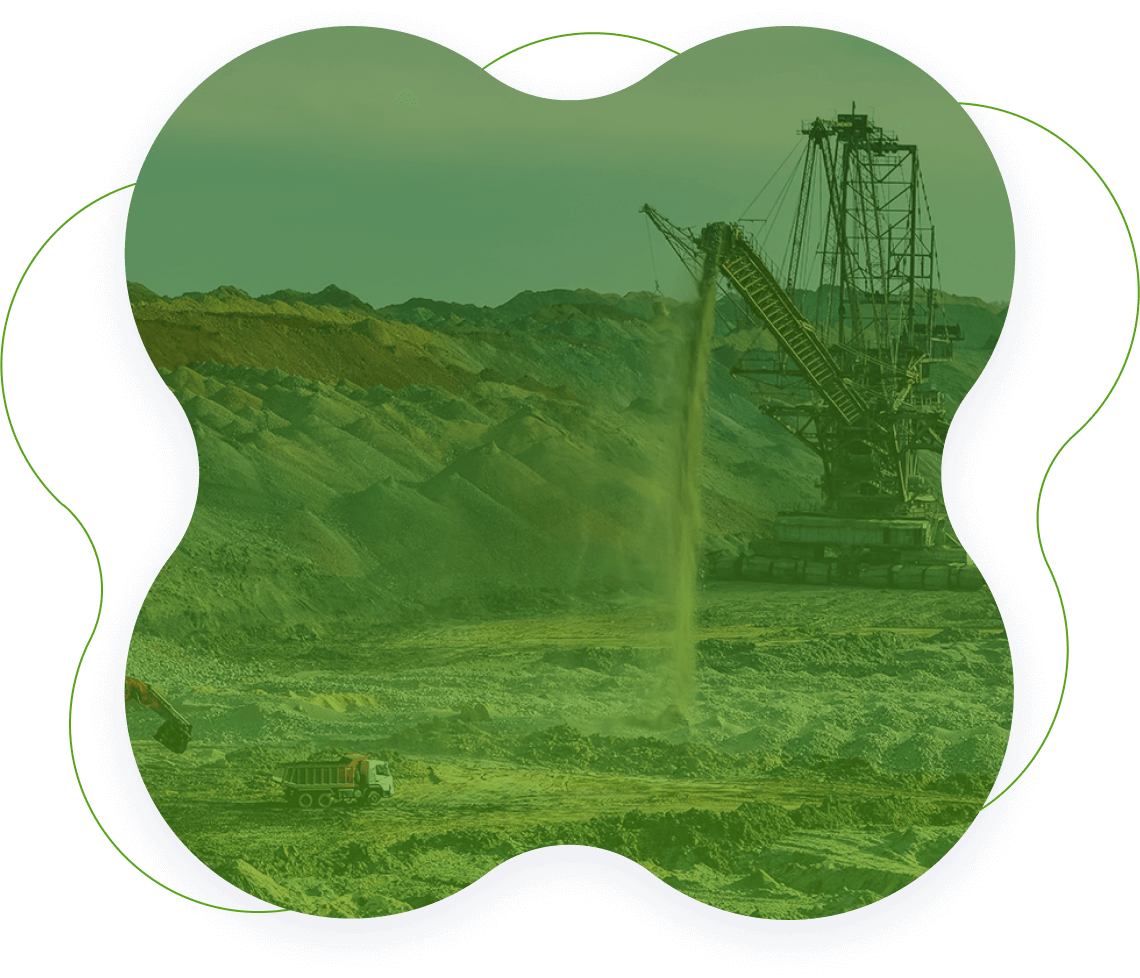
MDCplus, our top of the line industrial machine monitoring and production data collection system, brings the power of IIoT and AI solutions to the aerospace industry for improved equipment efficiency and reduced energy consumption
Reducing energy consumption by optimizing equipment operation
RESULTS ACHIEVED:- Real-time equipment monitoring system that meets modern requirements for environmentally friendly production
- AI solutions for predictive maintenance and tool wear predictions
- Increased equipment loading by 30%
- Annual savings of USD 0.3 million per year
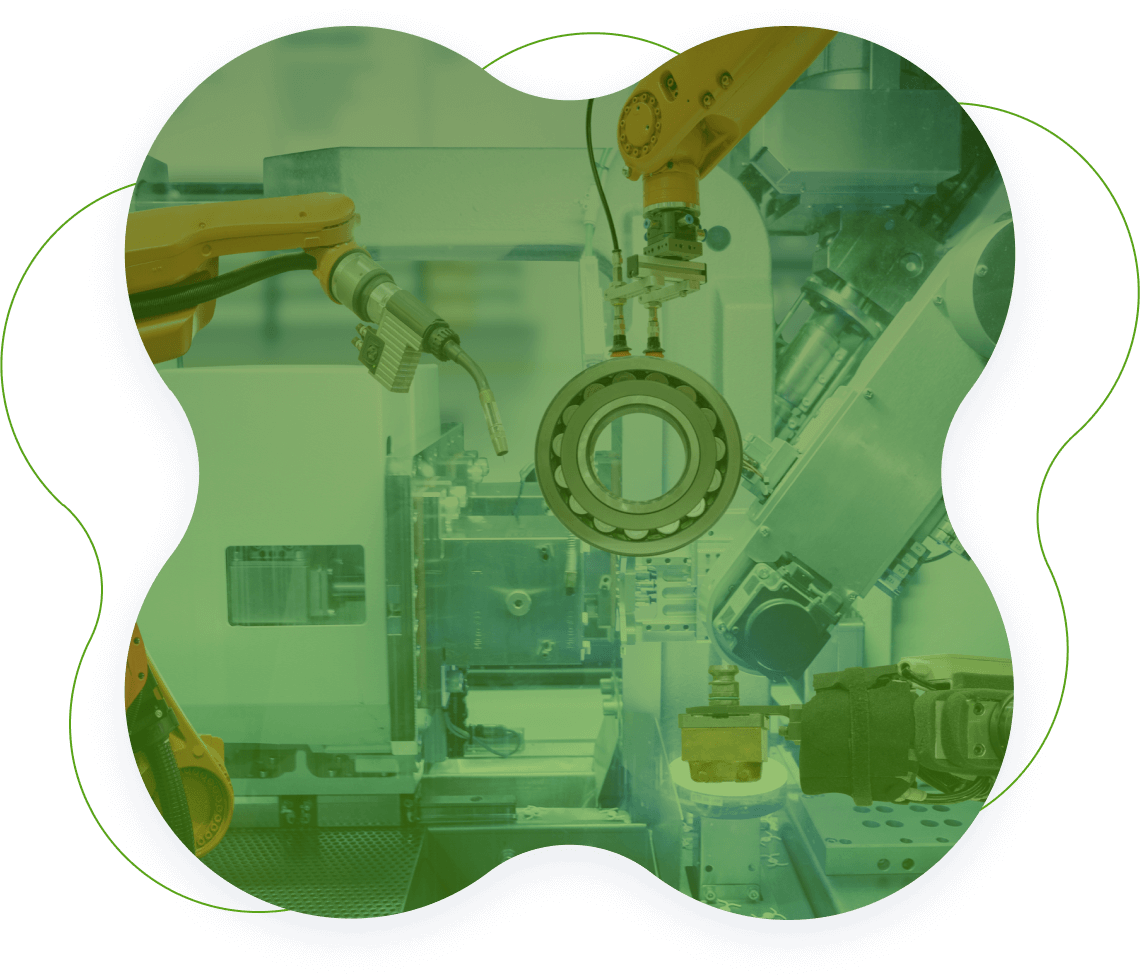
Taking care of the environment and industrial safety
Operational safety is just as important to us as the environment. Various solutions from Zyfra are built to improve efficiency and overall productivity and actively contribute to increased personnel safety.
Geonaft solutions specifically reduce the carbon footprint in hydrocarbon productions by reducing the number of required wells, the logistical load, total metal consumption, and the number of personnel in hazardous working environments.
Raising Health, safety, and environment (HSE) standards during the field development process by reducing the number of accidents, optimizing the volume of surface equipment, reducing the environmental impact, eliminating surface subsidence, removing radioactive sources, and well re-drilling.
Geonaft solutions also help the Oil&Gas Industry to efficiently utilize CO2 by calculating the locations and volumes for CO2 injection into the reservoir.
- >5000wells constructed using our software
- >400integrated drilling support service projects completed
- >40O&G operators and service clients
Potential decarbonization benefits from using digital solutions:
- 1Reducing operating expenses on electricity, logistics, and materials by 1-5%
- 2Reducing idling equipment times to 5-10%
- 3Carbon dividend* The monetary value of a ton of carbon has increased 167% between January 2014 and January 2021, and carbon trading markets have grown roughly 500% since 2017
- 4Loyal market
- 5Increasing business process efficiency through digitalization